Bending
We are happy to bend a variety of materials using our precision CNC press brake machine. We have some general guidelines below. If you have any questions on bending you can always reach us at
At a glance
- No minimum order quantity
- Not all of our materials are available for bending. Check the table below
- ± 1 degree bend tolerance
- ± 0.015" length tolerance
How Bending Works
We use a CNC press brake to create accurate bends in your sheet metal parts. The process presses your material between two specially shaped tools - a punch and a die - to create precise angles. Our CNC-controlled system ensures consistent, repeatable results across multiple parts. Here's a detailed look at how it works:
The Die
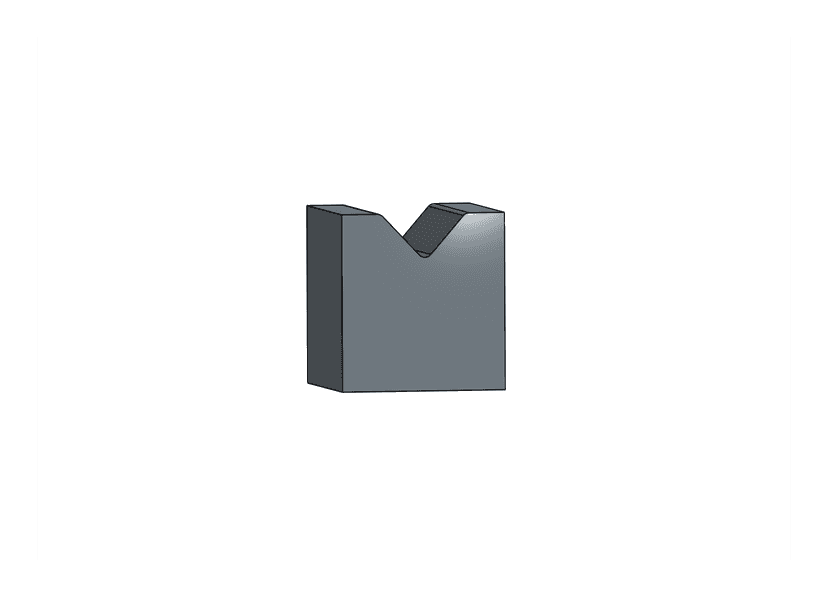
The die is the bottom tool with a V-shaped opening that supports and forms the material. Different dies are used for different materials and thicknesses.
The Punch
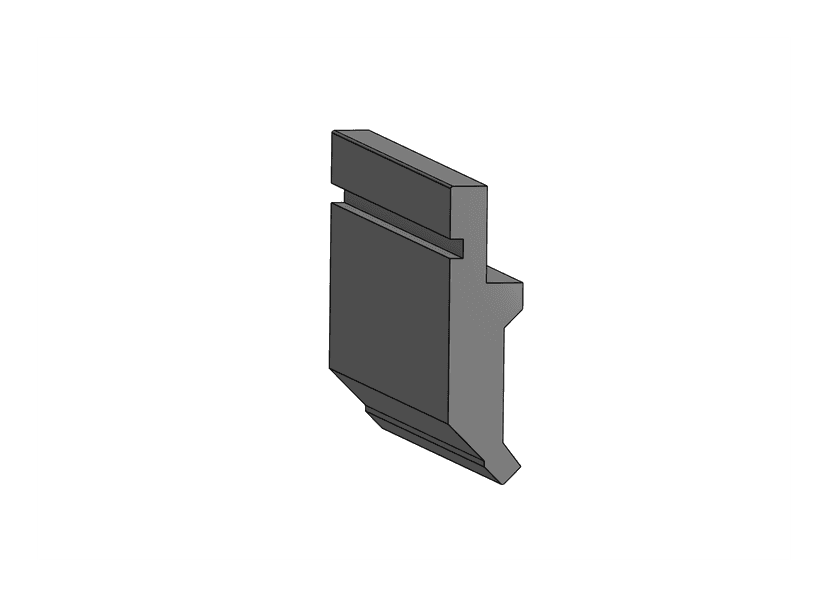
The punch is the top tool that presses the material into the die, creating precise bends. Its tip determines the inside radius of the bend.
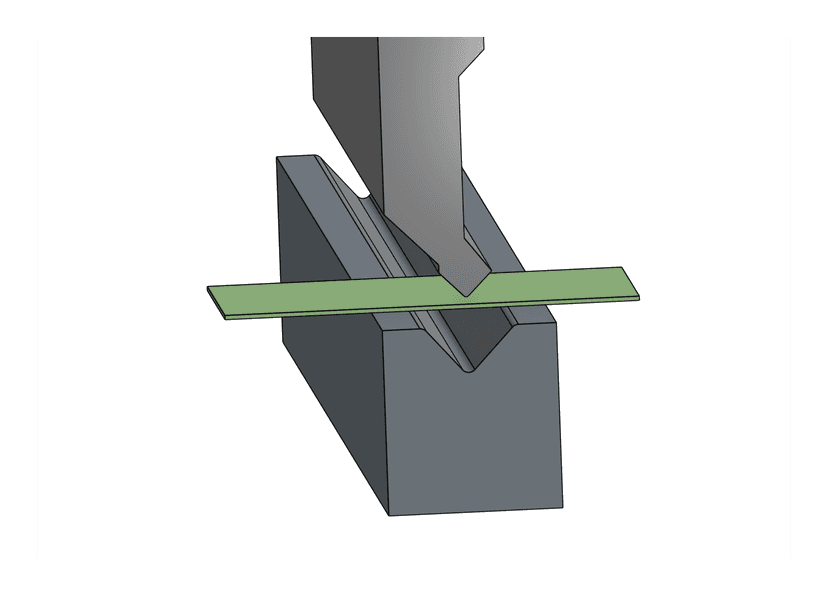
1. We position your part on the die using CNC backgauges so we know the bend is located properly

2. The punch descends and presses your part between the punch and the die, forming the correct angle.
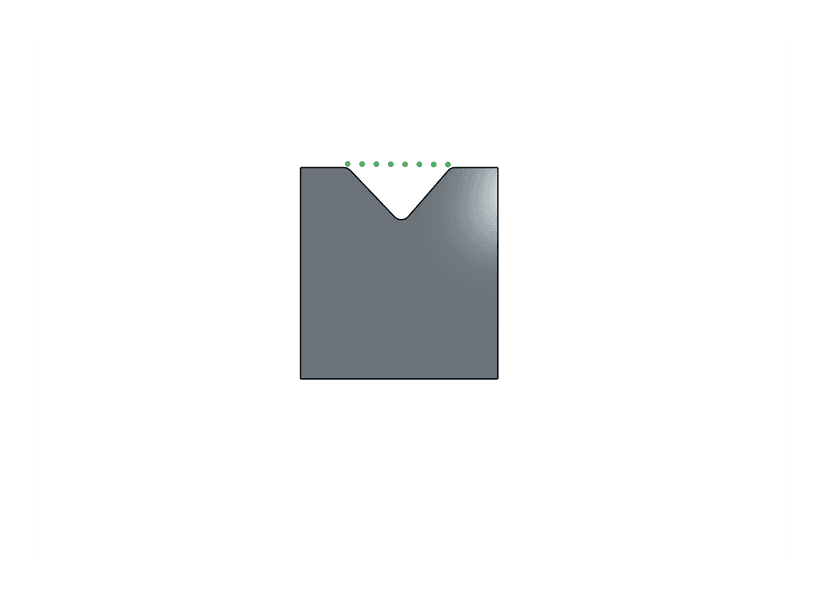
Good to know: Die Opening / Die Width
When designing your parts for bending, you should consider the die width. The die opening (or die width) is the distance between the two sides of the V-shaped die.
Features within one die opening distance from the bend line may be deformed during bending.
Flanges that are too close to the bend line may be deformed during bending. The part needs to be fully supported by the die on either side of the bend line to form properly
Angles
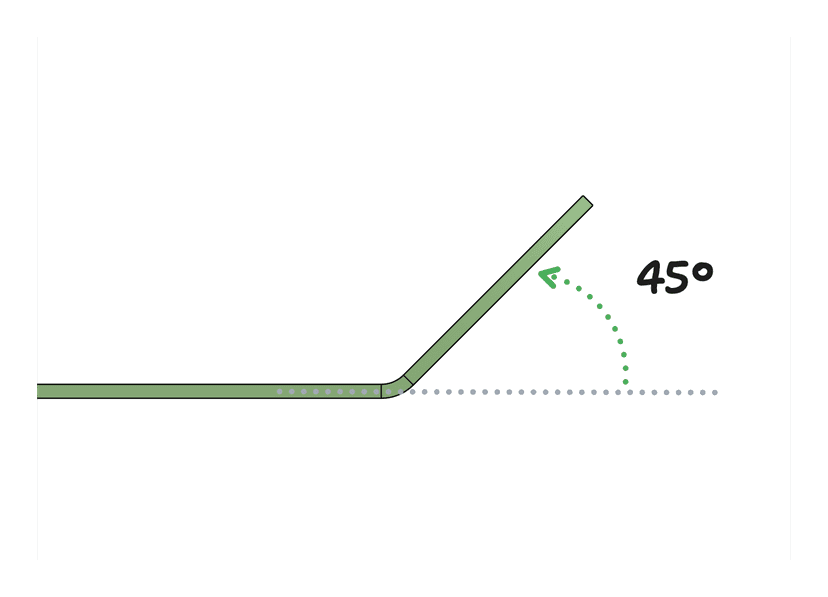
How We Measure Angles
Bend angles can be confusing at first glance. While the example might look like a 135° angle, it's actually a 45° bend. Here's why:
- Bend angles are measured from the original flat position (shown by the gray line)
- The angle represents how far the flange was bent up from flat
- In this case, the flange was bent up 45° from its original flat position
This is the standard way bend angles are measured in sheet metal fabrication. We handle showing the correct angle by default when you upload your .STEP file
We can create bends from 1° up to 90°. Angles greater than 90° or hemmed edges are not possible with our current tooling.
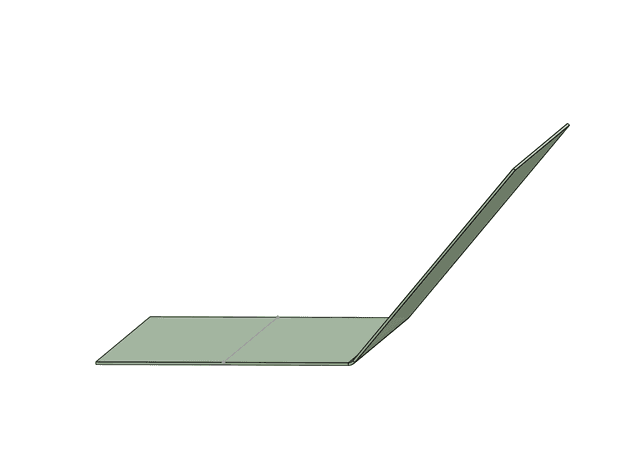
50° bend - A typical acute angle bend
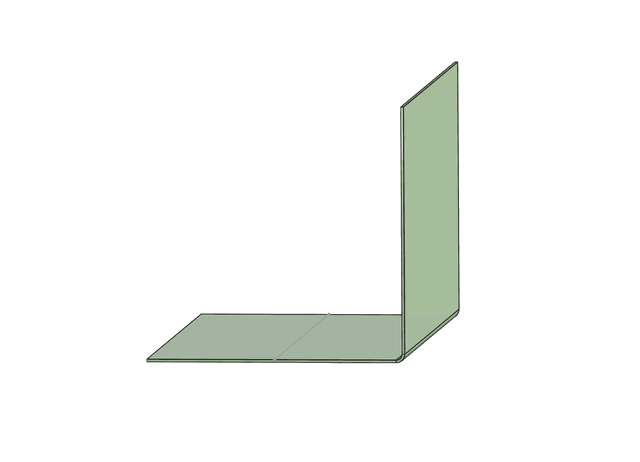
90° bend - The maximum angle we can achieve
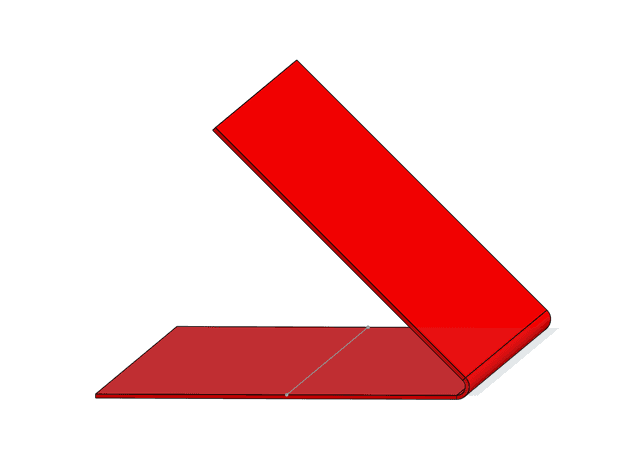
135° bend - Angles over 90° cannot be formed
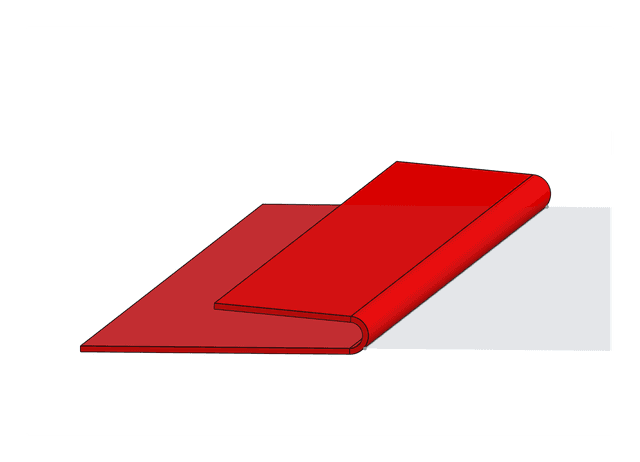
Hemmed edge - We cannot create hemmed edges
Flange Length
The flange length (the part being bent up) must be long enough to be properly supported by the die during bending. Insufficient flange length can lead to distortion and inconsistent bend angles.
Before Bending
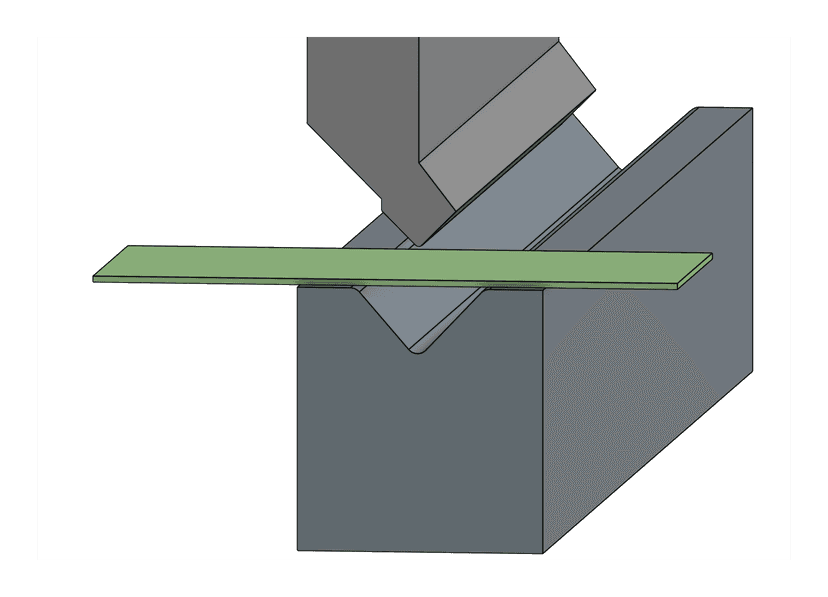
✅ Flange fully supported by the die before bending
After Bending
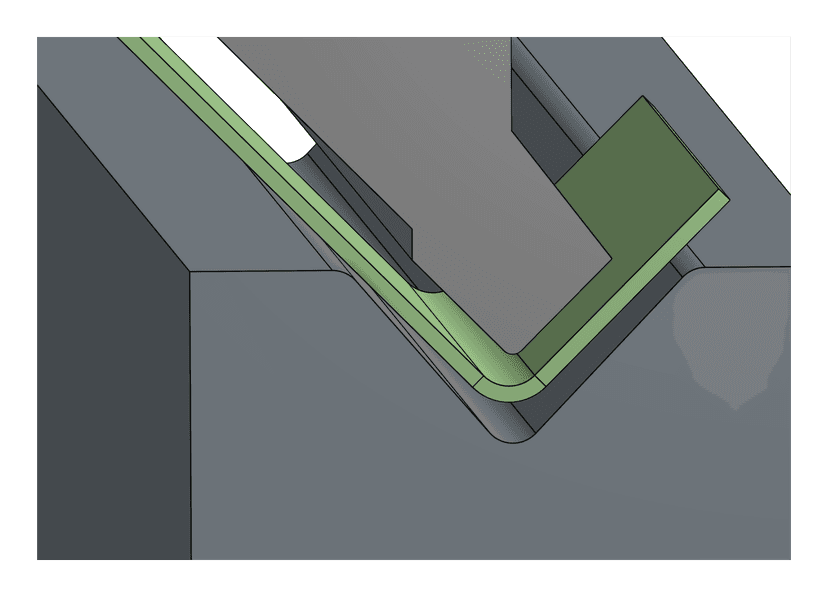
✅ Results in a clean, accurate bend
Before Bending
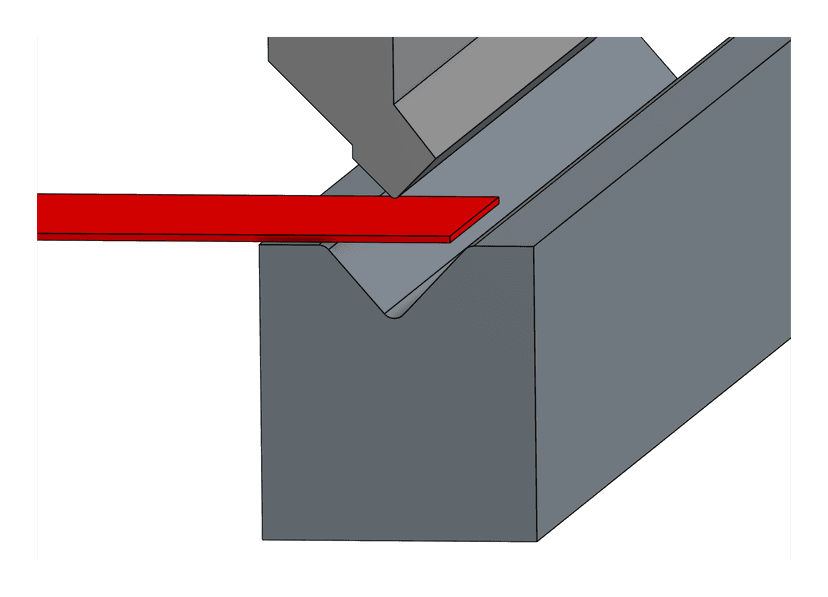
❌ Flange not fully supported by the die
After Bending
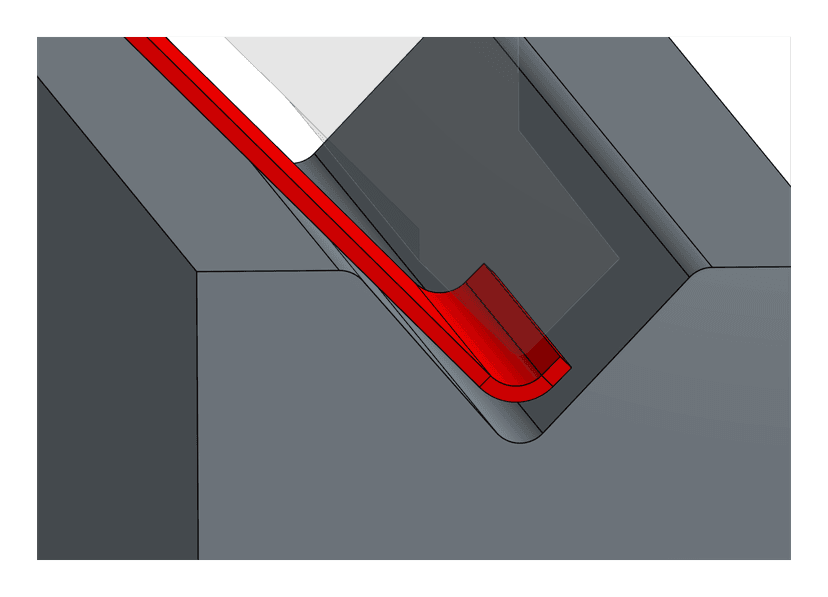
❌ Results in distortion and inconsistent bend angle
Design Tip: The minimum flange length depends on your material thickness. As a general rule, aim for a flange length at least 4 times the material thickness to ensure proper support during bending.
Distortion
Feature distortion occurs when holes, slots, or other features are placed too close to a bend line. To prevent distortion, keep features at least ½ the die opening distance away from any bend line.
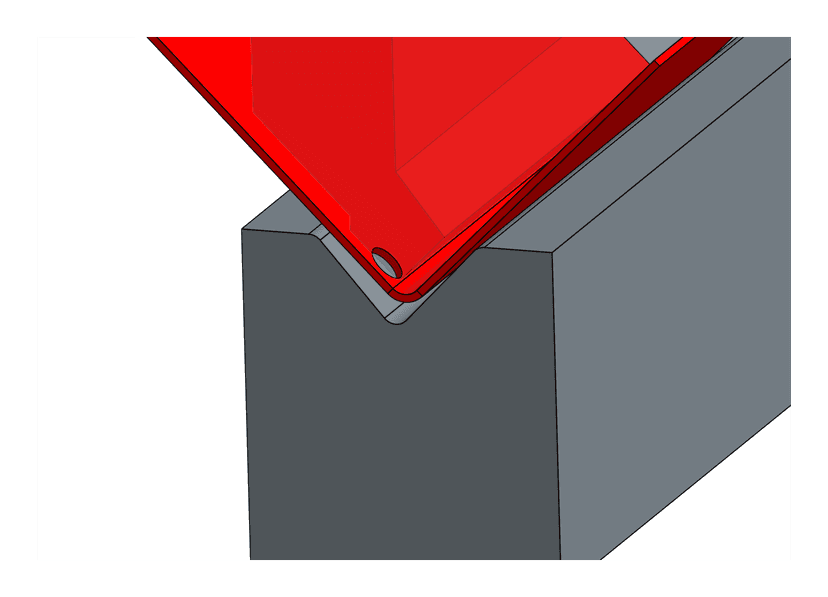
❌ This hole is within the die opening distance and will become oval-shaped during bending
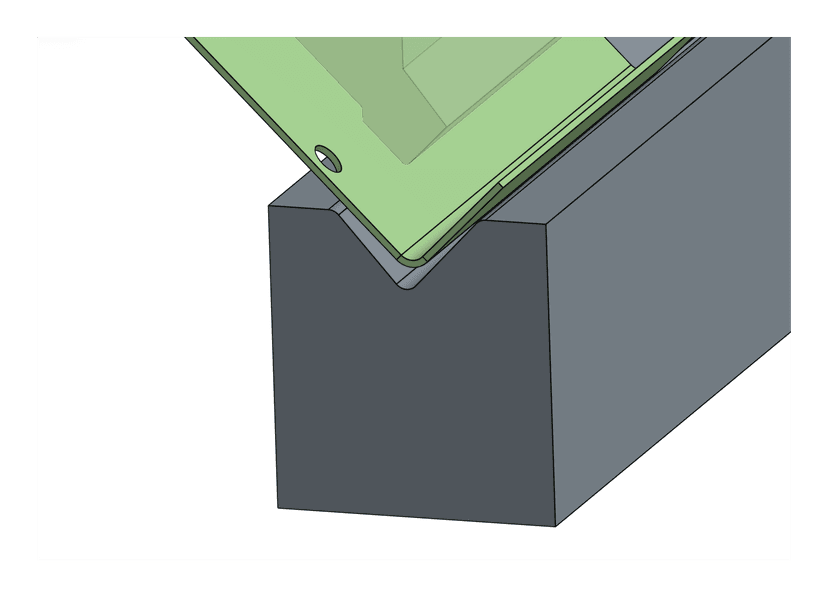
✅ This hole is safely outside the die opening distance and will remain round
Design Tip: When designing your part, consider the material thickness. Thicker materials require larger die openings, which means features need to be placed further from bend lines.
U-Channel Design
When designing U-channel parts (parts with two parallel bends), the ratio between the base and side flanges is crucial. A 3:1 ratio between the base and flanges helps prevent tool collision and ensures consistent bending.
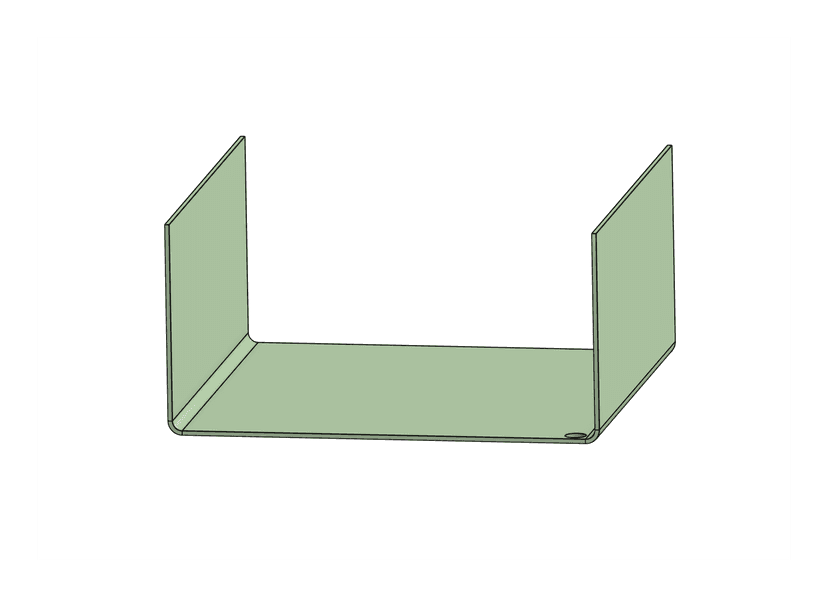
✅ Base is 3x longer than flanges, allowing easy tool access
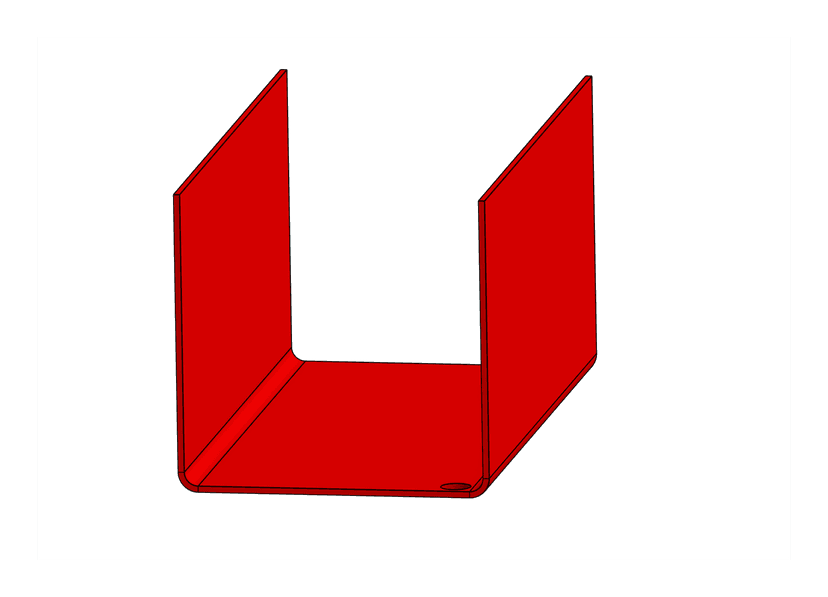
❌ Base too short relative to flanges, making bending difficult
Tool Collision
When U-channels are too narrow, the punch can collide with the already bent flange. Here's what that looks like in profile and in 3D:
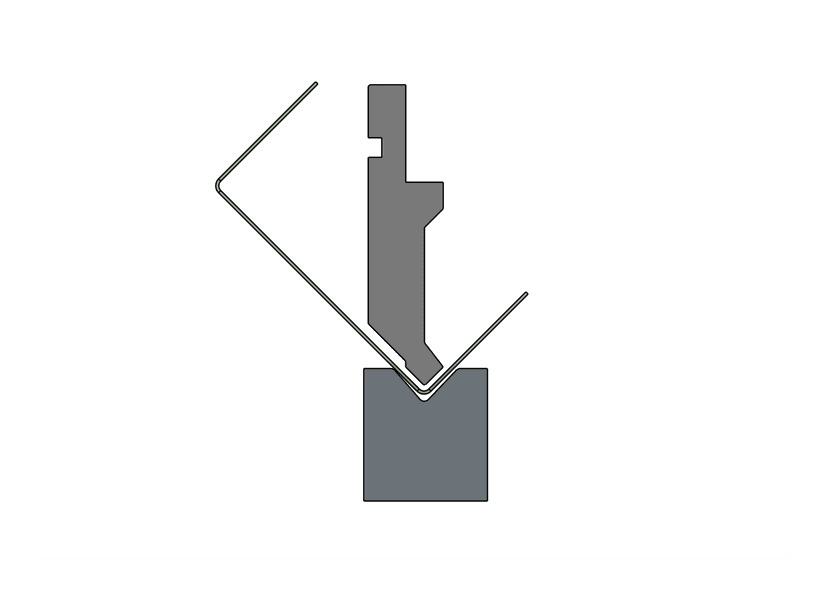
✅ Sufficient space between punch and first bend
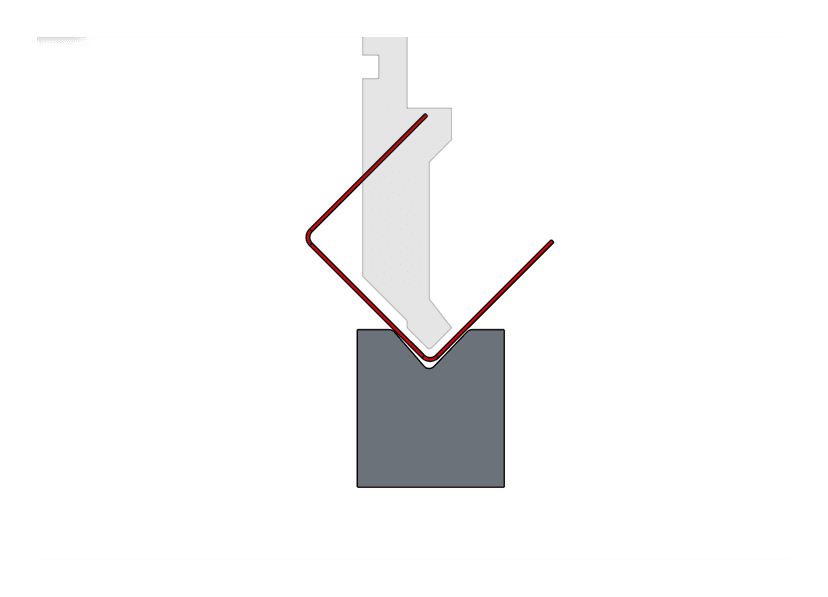
❌ Punch collides with first bend during second operation
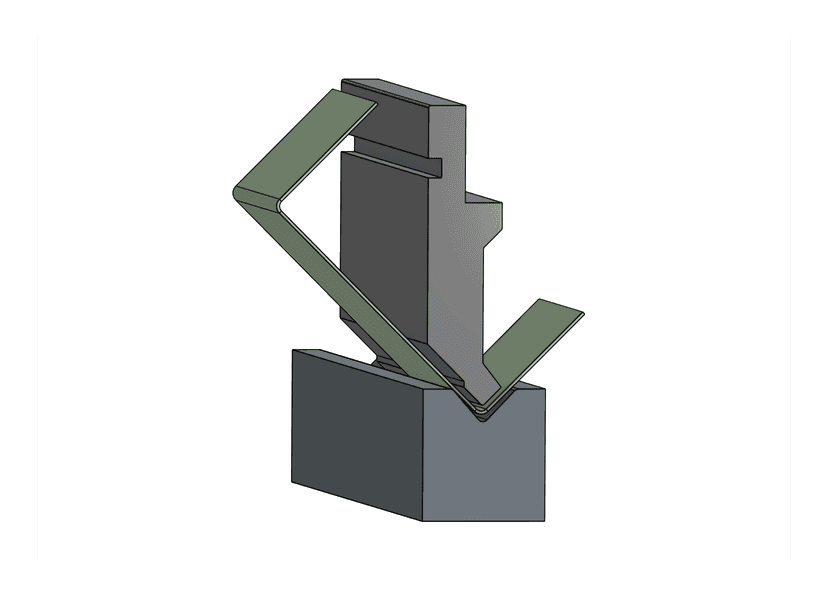
✅ 3D view showing proper tool clearance
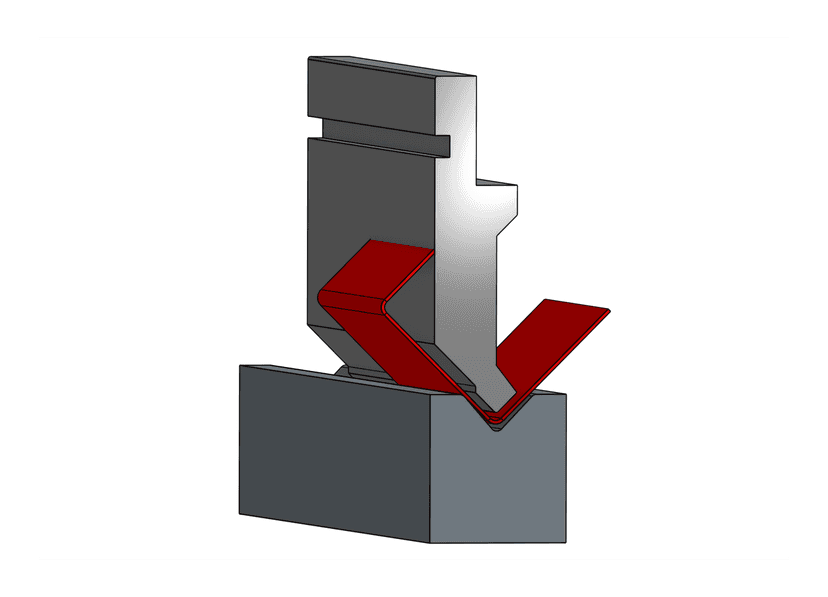
❌ 3D view showing tool interference
Design Tip: When designing U-channel parts, aim for a base length at least 3 times the height of your flanges. This ensures proper tool clearance and consistent bend quality.
Questions About Your Design?
We automatically review all parts for manufacturability when you submit them. If we spot any potential issues, we'll email you right away with suggestions.
Can't find what you're looking for? Have questions about your design? We're happy to help! Reach out anytime at